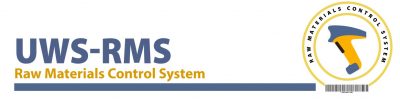
FREQUENTLY ASKED QUESTIONS
General Questions about the System
Please send us an email to sales@weighingcontrol.com including your address and phone number. We will send your information to one of our distributors and ask him to contact you immediately.
ROI usually varies from one company to another. We have customers that have seen their investment recovered in one month. But in average, we could say the ROI should be of three months after the system begins operating.
- Our system offers so many advantages it would be hard to explain them all without making this answer too extensive. Here is a brief description of the major advantages vs our competitors.
- On-site raw material control: Many companies offer a software solution to track down inventories, but they are based on theoretical raw materials entries and deliveries to production. There is no equipment in the warehouse floor that validates and registers the material input/output.
- Adaptation of existing peripheral devices: In many cases, existing devices such as the PC, scanners and label printers can be adapted to our system. WCS does not force the customer to purchase new equipment. Furthermore, if your company requires new devices, our distributors can quote them and sell them to you, but you are not force to purchase them from us.
- Raw Materials Quality Control Module: We offer a customized Quality Control module that lists, registers and validates the quality control tests you need to make for the raw materials received. This option generates automatic reports of the tests made to each raw material, supplier, supplier’s lot number, among other valuable information.
- Real time reports: The system registers in the warehouse the entrance/exit of material through bar code label generation/scanner validation. The information update is immediate and can be seen on the network PC located in the company’s administration office.
- Flexibilty/Customization: We offer customization to the standard version of our system to adapt it to your company’s/industry specific requirements.
- Competitive prices: Our customization prices are significantly lower than regular customization prices offered by software /ERP companies.
- All sales are made through our distributors. Our distributors are authorized companies with a background in the weighing industry that are familiar with enterprises general concerns and needs, including the warehouse, quality control, production and shipment areas. They will discuss your materials receiving process and present you the best solution according to your requirements. When you place the purchase order, they will send us the system request, including the customized modifications required. When we finish the system, we will send it over to them. They will install it and train you in the proper operation of the system.
- Your distributor has been trained for configuring the system, answering operation questions, solving communication failures and some other common problems that might arise while learning how to use the system and adapting to continuous operation. They also have Weighing Control Systems full support in case they might have technical questions to uncommon operating dilemmas.
- Yes. We usually recommend our customers to use the system for at least two or three months before requesting software modifications/ system operation changes. This period of time helps customers get familiarized with the system, identify the most important benefits it offers to the company and determine a more accurate ROI period for their company. It also helps identify and determine which modifications are really necessary to improve the operation in their company.
- No. The raw materials need to be labeled by the UWS-RMS Raw Materials System in order to be validated by the Manual Batching System. A specific format label is required.
- The main peripheral devices required are a barcode reader and a barcode printer. The number of barcode scanners though, might vary according to your actual receiving/dispatching material operation. For example, if you have only one door for entrance/exit of material, you will only require one label printer and one scanner. But if you have several entrance doors, you might want to place one printer with a network PC for each door.
- We commonly use Datamax printers and Symbol and PSC bar code scanners.
- The system is configured according to your needs. So, if you need to print one label for each drum, one label for each pallet, and one label for each complete or partial purchase order received, it can be done.
- Again, since our system is very flexible, we can include as much information as you need. Common information included is the raw material name, lot number, supplier, total weight, date received, expiration date, etc.
Software related questions about the System
- Raw Materials Current Levels.
- Historical Record of Raw Materials received by date.
- Historical Record of Raw Materials received by item.
- Historical Record of Raw Materials delivered by date.
- Historical Record of Raw Materials delivered by item.
- Historical Record of Raw Materials received by supplier.
- Raw Materials Purchase Orders.
- Raw Materials Delivery Orders.
- Raw Materials Catalog.
- System Modifications.
- No. The system can store an unlimited amount of ingredients in the System’s software.
- The number of suppliers that can be handled by the system is also unlimited.
- It depends on the amount of raw materials each company has. Nevertheless, they can be imported from text files. This procedure has to be done only once during software installation. After that, the catalogs only need maintenance.
- Once again, the system can handle an unlimited amount of receipt orders. If the order is not completed, it will not be registered in the system until all the raw materials listed in such order are received and registered.
- Yes. As a matter of fact, the system can record the supplier raw material lot number, and if desired, a new lot number can be assigned after tests have been done to the materials.
- Yes. Customized automatic import/export can be done at an additional cost in most cases. It is also possible to make periodical data imports if the file is in txt format and follows a predetermined data sequence, provided by WCS, in order for data to be imported correctly.
- Yes. It is possible to save the information and export it to excel, access, or as a text file. Customized automatic import/export can also be done at an additional cost in most cases.
- Software upgrades are usually available every two years and the cost varies from 25% to 40% of the original price paid for the software, depending on the version you want to upgrade from.
- NO. The historical data limit depends on the PC hard disk capacity because the database is divided by monthly files.
- Yes. You can install and run other applications in the PC while using the UWS-RMS system.
- The number of users is unlimited, but only one at a time can be modifying data per module.
- The system has 4 level access rights. One level grants complete access to the system, while the following levels have different restriction access rights.
Installation and Operation related questions about the system
- The system requires minimum training. Training usually lasts two to three days. The first day is dedicated to theoretical training: the operation course is given in 4 hours. The maintenance course is given in 3 hours approximately. The following two days are used to supervise the operation of the system and solve any question that might arise.
- The easiest way is to email your distributor. He will be able to answer your email solving the questions you have.