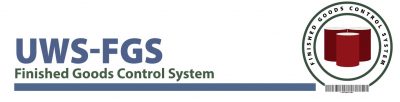
FREQUENTLY ASKED QUESTIONS
General Questions about the System
- Operator’s decisions elimination: The VIC-6000 controller receives from the PC the programmed filling orders, including target weight and tolerance range per product to be filled. This eliminates any decision taking by the operator, and thus eliminates possible mistakes.
- Automatic Cut: The filling of each container is controlled by weight. When the target weight is reached, the VIC6000 controller closes the valve to stop material addition.
- PC Filling Scheduling: The system allows filling orders to be programmed. Scheduling can be done per shift, day, week, etc. Up to 300 Fill Orders can be placed at a time.
- PC Filling Products management: The system stores in the PC the different products to be filled, including product name, target weight, tolerance range, etc. The system administrator can modify the quantity to add per container at any time without having to make any programming.
- Complete Traceability: The information of the filling process is stored in the non volatile memory of each of the VIC6000 controllers and it is continuously retrieved by the remote PC for its consolidation. This gives complete traceability of the filling process (filling cycle times, materials consumptions, fill orders finished, etc.).
- Inventory and Delivery Control Module: Includes a software module for complete control of Finished Goods Inventory (inputs, outputs, real-time stocks), filled containers entrance registration into the finished goods warehouse, shipping orders generation, shipping goods validation and registration for delivery control of finished goods to customers.
- Real Time Reports: The system registers each event taking place in the filling station: date, time, containers filled, quantities, labels generated, pallets finished, etc. Eight standard reports can be generated with the UWS-FGS software with real time information. The information can be exported to other applications for further manipulation, like Microsoft excel and access.
- No programming required: Our system is always delivered ready to use. It is not necessary to program the controllers for a specific operation sequence or even to program set point values.
- Adaptation of existing peripheral devices: In many cases, existing devices such as the PC, scales, weigh modules, sensors, valves, etc. can be adapted to the UWS-FGS system.
- Flexibility/Customization: We offer customization to the standard version of our system to adapt it to your company’s/industry specific requirements.
- No dedicated PC required: The PC where the software is resident can be used to run other applications. The UWS-ABS system demands only standard PC resources.
- Windows Network Operation: The system supports network operation, for different users to access it from different PC’s.
- Competitive prices: Our standard system and customization prices are significantly lower than regular filling systems offered in the market.
- Scalability: The system offers integration with any of the UWS-Series platform.
- The return of investment varies depending on the industry and the production control used prior to the installation of any of the UWS Series Systems. In our experience, the ROI has never exceeded one year.
- The standard information included in the label is: Company, Date, Time, Product Name, Net Weight, Lot Number, Fill Order Number, and barcode. Additional information can be included such as operator, expiration date, filling line, etc.
- The restrictions are: Minimum label size: 2.25”W x 2”L; Maximum label size: 4” x 6”)
- Yes. The system can print an automatic ID label each time a pallet is completed.
- Yes. It is an automatic filling system but only for industrial containers (totes, drums, cubes, etc.) based on weight not volume and one container at a time. It is not intended to be a high speed filling system.
- The UWS-FGS:
- Controls the correct amount filling.
- Generate and ID label per container.
- Keeps digital record of historical filling information.
- Includes reports and the capability of exporting data to other applications.
- Yes. We can develop an interface adapter between the PC software-hardware with your filling machine as an option.
- Smallest: Cubes of 5 gallons. Largest: Limited by the scale capacity and size.
- Please send us an email to sales@weighingcontrol.com including your address and phone number. We will send your information to one of our distributors and ask him to contact you immediately.
- Yes. Customization is always an option. The price of the customization will vary depending on the simplicity or complexness of the modification requested.
- Yes. We usually recommend our customers to use the system for at least two or three months before requesting any customizations. This period of time helps customers get familiarized with the system and also identify which modifications are really necessary to improve the operation in their company.
- All sales are made through our distributors. Our distributors are authorized companies with a background in the weighing industry. They are familiar with enterprises general concerns and needs, including the quality control, production and shipment areas. They will discuss your filling requirements and offer you the best solution.
- A CD with the UWS-FGS software, maintenance and operation manuals.
- A hardware key.
- At least one VIC6000 controller and up to 32 controllers, depending on the amount of controllers purchased.
- Peripheral devices purchased, if any (scanners, printers, scales).
- Your distributor has been trained for configuring the system, answering operation questions, solving communication failures and some other common problems that might arise while learning how to use the system and adapting to continuous operation. They also have Weighing Control Systems full support in case they might have technical questions to uncommon operating dilemmas.
- Yes. The UWS-ABS Automatic Batching Control System, as well as any other module of the UWS Series can be integrated into one solution for complete production process control, from raw materials receiving to finished goods shipment.
Operation related questions about the system
- The system is installed by the distributors. Preinstallation instructions are sent to the customer as soon as the system has been purchased. Preinstallation instructions are done by the purchaser. Some distributors are willing to do the preinstallation instructions. If you are interested, ask your distributor if he can carry out the preinstallation instructions and how much it would cost.
- The network cable can have up to 4,000 ft.
- No. Specifications of the cable required are given once the system is purchased. The cable installation is usually done by the purchasing company personnel. If desired, though, the cable can be provided by the distributor. Some distributors are also willing to quote and install the network cable.
- It depends on the wireless modems connected. Typical range with the standard 6” antenna is 1000 ft to 2000 ft. This distance can be greater with line of site.
- Since the system is very friendly, regularly only one day is required for hardware operation, software operation, troubleshooting and maintenance courses. Training can take longer if a large group of operator’s (more than five) needs to be trained, though.
- The easiest way is to email your distributor. He will be able to answer your email solving the questions you have, or if he thinks it might be something a little bit more complicated, he can give you a call and schedule an appointment.
Software related questions about the System
- In the standard version, 3000 different products and sizes can be stored. Modifications can be made if more products storage is needed.
- 500, but if a specific application demands more than 500 fill orders at a time, modifications can be done to adapt the application to the customer’s specific requirements.
- It depends on the amount of products and sizes each company has. Nevertheless, they can be imported from text files. This procedure has to be done only once during software installation. After that, the catalogs only need maintenance.
- Yes. Tolerance can be set either in % or in quantity and can be changed in the UWS-FGS Software at any time. Each product can have a difference tolerance.
- Yes. Customized automatic import/export can be done at an additional cost in most cases. It is also possible to make periodical data imports into the UWS-FGS software if the file is in txt format and follows a predetermined data sequence (provided by WCS) in order for data to be imported correctly.
- Yes. It is possible to save the information and export it to excel, access, word, or as a text file. Customized automatic import/export can also be done at an additional cost in most cases.
- No. All the historical information generated in the VIC controllers is stored in the PC in a .dat format, which demands very little space in the hard drive. If the hard drive of your PC has 100 mb available, you shouldn’t have any problems storing one year’s worth information.
- Historical Record of Filled Products by Date.
- Historical Record of Filled products by Item.
- Historical Record of Shipped Products by Date.
- Historical Record of Shipped Products by Item.
- Finished Products Inputs by Date.
- Finished Products Inputs by Item.
- Fill Orders sent
Shipping Orders sent. - Theoretical vs. Real by Filled Product.
- Finished Products Current Levels.
- Products Catalog.
- System Modifications.
- The UWS-FGS system runs under Microsoft Windows® operating system.
- Software upgrades are usually available every two years and the cost varies from 25% to 40% of the original price paid for the software, depending on the version you want to upgrade from.
- Yes. You can install and run other applications in the PC where the UWS-FGS software is resident. The UWS-FGS application needs to be open at every time for historical information update in the PC. If in the evening the PC is turned off, historical information will be kept in the VIC6000 controller’s non-volatile memory, until the PC is turned on again.
- Only one user can modify catalogs at a time and up to 10 users can view reports from any LAN PC.
- The software has four level access rights, ranging from complete access rights to data consulting only. The VIC6000 controller offers only one level access and thus, every operator has the same access rights. Supervisors, though, have an additional and unique password that allows them to delete, pause or duplicate a filling order and accept ingredients out of tolerance.
Hardware related questions about the System
- Two PC’s: one for the Filling Process area and one for the Finished Products warehouse.
- One or more VIC6000 controllers.
- One, two or up to three scales per controller.
- Instrumentation devices such as valves, pumps, motors (if required).
- One printer for automatic ID label generation per product filled.
- Up to 32 VIC6000 controllers can be installed in the same network.
- Almost any brand of electronic scale with an RS-232 serial port can be adapted to the system. Regarding printers and scanners, we rather work with Datamax printers and Symbol and PSC bar code scanners.
- Any pneumatic or electrical open/close valve.
- Yes. The Filling Stations are completely independent. If you have 5 filling stations, all of them can be working at the same time. Each one receives from the PC the Filling Orders to be fulfilled.
- The controller is intended for heavy duty and industrial environment. That is the reason for the stainless steel NEMA 4X enclosure, but not for washdown environments.
- Main board
- Fluorescent Display
- Power Supply
- Membrane Keypad
- RS-485 communication board
- USB Hardware key
- Spare parts are sold by your distributor. They usually have a small inventory of the most important components of the VIC6000 controller. If for some reason the distributor is out of stock, the lead time should be of one week approximately.
- To ensure the continue operation of the system, preventive maintenance is recommended to be done every six months.
- The only component that suffers the most is the membrane keypad with a lifetime average of 3 years at normal conditions work, with appropriate maintenance.
- Yes. Rs232 wireless modems can be connected to the controller and pc.
- Yes. But every cabinet should be installed with a purging system.